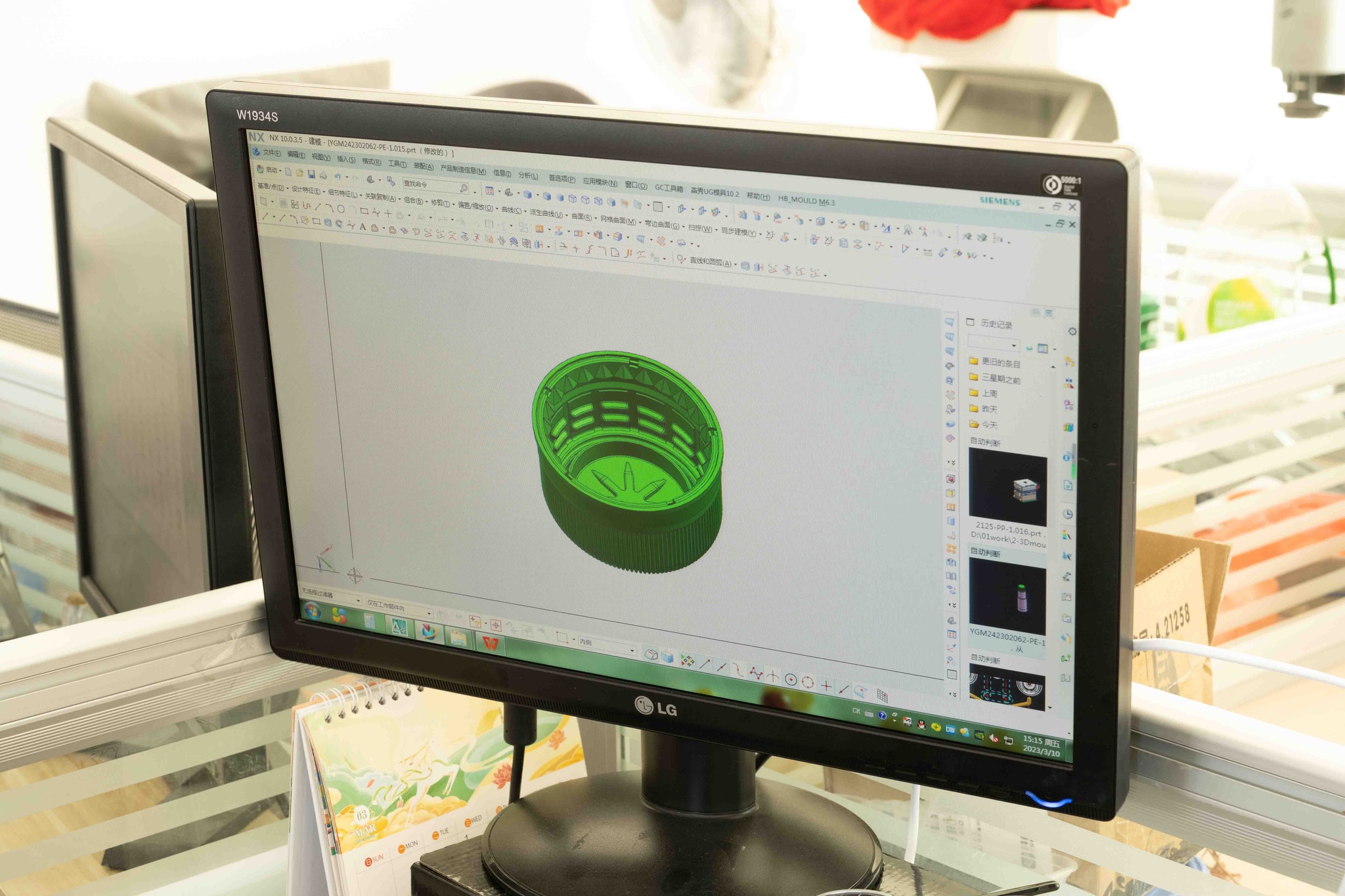
Bottle Cap Design and Manufacturing: A Guide to High-Quality Cap Molds
Introduction
Bottle cap design and manufacturing play a crucial role in the packaging industry, ensuring product safety, convenience, and brand appeal. Whether for mineral water bottles, beverage caps, or pharmaceutical packaging, a well-designed bottle cap mold is essential for mass production. This article explores bottle cap design principles, manufacturing processes, and the role of a professional cap mold factory in delivering high-quality solutions.
Key Factors in Bottle Cap Design
1. Material Selection
Most plastic bottle caps are made from:
Polyethylene (HDPE/LDPE) – Common for water and beverage caps.
Polypropylene (PP) – Used for hot-fill applications due to heat resistance.
PET – Lightweight and recyclable, ideal for eco-friendly packaging.
2. Functional Design Considerations
Leak-proof & Tamper-evident Features – Ensures product safety.
Thread Design – Must match the bottle neck for a secure seal.
Ergonomics – Easy-to-open caps improve user experience.
3. Aesthetic & Branding Elements
Custom Colors & Logos – Enhances brand recognition.
Textured or Embossed Surfaces – Improves grip and visual appeal.
Bottle Cap Manufacturing Process
1. Mold Design & Engineering
A cap mold factory uses CAD/CAM software to design precision molds. Key steps include:
3D Modeling – Ensures accurate dimensions.
Flow Simulation – Optimizes plastic injection for defect-free caps.
Prototype Testing – Verifies functionality before mass production.
2. Injection Molding
High-speed molding machines produce thousands of caps per hour.
Automated Ejection Systems – Ensure consistent quality.
3. Quality Control
Dimensional Checks – Confirms thread accuracy.
Pressure & Leak Tests – Guarantees seal integrity.
Choosing the Right Cap Mold Factory
When selecting a bottle cap mold manufacturer, consider:
✔ Experience in Cap Mold Production – Look for factories specializing in plastic injection molds.
✔ Advanced CNC Machining – Ensures high-precision molds.
✔ Customization Options – Ability to design unique cap shapes and features.
✔ Quality Certifications – ISO 9001 compliance ensures reliability.
Conclusion
A well-designed bottle cap mold is critical for efficient, high-quality production. Partnering with an experienced cap mold factory ensures durability, functionality, and brand consistency. Whether for water bottles, beverages, or pharmaceuticals, investing in precision molds guarantees superior packaging performance.